Most of the time, electricity is there when we need it. A flip of a switch and the lights turn on. A click of a remote control and the television starts up. A press of a button and your bread starts toasting. Now consider everything that has to work for electricity to be taken for granted. While it is a miracle of the modern world, nothing about this is magic: it takes a lot of physics, engineering, and innovation for the electric grid to be safe, reliable, and resilient. Remove any of those qualities, and it only takes a nanosecond before we notice its absence.
Decarbonized and affordable are two other qualities that will only become more important in the race to reduce greenhouse gas emissions by 50 percent by 2030, in accordance with the Paris Agreement. And as the built environment and transportation sector rely less and less on fossil fuels over time, investments in the electric grid will need to keep pace with increased demand. Renewable energy, which keeps getting cheaper to install than polluting sources, will continue to account for most new generation added to the grid. Power Plant Transformer
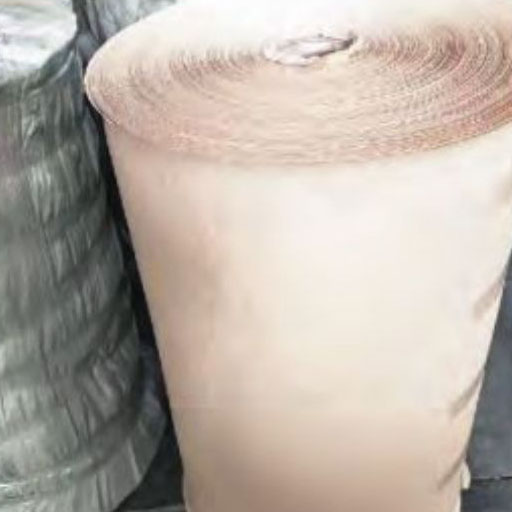
But the cleanest—and cheapest—energy of all is that which is never produced or consumed to begin with, which puts energy efficiency at the top of the list of climate solutions. While energy efficiency may be most commonly considered in the context of buildings, the electric grid can be made more energy efficient as well. Among the scores of products covered by appliance and equipment standards developed and promulgated by the U.S. Department of Energy (DOE) are distribution transformers. Transformers are essential for a functional grid. Before electric power coursing through transmission lines can be delivered to a home, a distribution transformer is needed to lower its voltage. There are more than 50 million distribution transformers across the U.S. electric grid, and about 70 percent of them have been in service for 25 years or more.
Even more transformers will be needed as the grid grows up to three times larger to support decarbonization at scale. Modern equipment—mostly made with cores of grain-oriented electrical steel—already fares pretty well: less than two percent of all electricity generated is lost due to distribution transformer inefficiency. But to the extent each new distribution transformer is more energy efficient, even by a little, savings in the aggregate will be significant over time. Increasing transformer efficiency will require new technologies and materials, which are at the center of the latest DOE proposal to update standards for this workhorse piece of equipment.
In late 2022, DOE proposed new standards for three categories of distribution transformers that would save more than 10 quadrillion British thermal units (quads) of energy (for comparison, the United States used about 100 quads in 2022) and $15 billion over 30 years, as well as lower carbon dioxide emissions by 340 million metric tons (the equivalent of closing 90 coal-fired power plants). Greater use of amorphous steel, in addition to grain-oriented electrical steel, would make such savings possible. About 22 million distribution transformers with amorphous steel cores are already in widespread use in Canada and in parts of Europe and Asia.
This brings us to Metglas, Inc., based in Conway, South Carolina. If the proposed energy efficiency standard is finalized, Metglas would be the source of a lot of the amorphous steel necessary for the next generation of distribution transformers. “Simply put, we offer the most energy-efficient, environmentally-friendly transformer core materials, which are found in transformers around the world,” said Metglas Chief Executive Officer Rob Reed. To meet future U.S. demand driven by updated standards, Metglas is in the process of a massive scale-up operation to increase manufacturing capacity to 45,000 metric tons of amorphous steel over the next two years, with more room to grow.
Amorphous steel was invented in the 1970s for use in distribution transformers and provides at least 60 percent reduction in no-load loss compared to conventional materials. Metglas estimates that installing one of their 750 kilovolt-amp, three-phase transformers (capable of serving up to 10 electric vehicle charging stations) would deliver 6,600 kilowatt-hours of energy savings per year, which is enough to power an average U.S. home for seven months. Multiply these energy efficiency gains by the number of transformers that need to be replaced or installed in the next few decades, and the climate benefits start to add up to very big numbers.
A Metglas distribution core made of amorphous steel. Credit: Metglas
These impressive savings are balanced to some degree by other important considerations. For example, Metglas reports that amorphous steel contributes to higher upfront costs for transformers but lower total ownership costs, which has made it more competitive in countries with more expensive energy. “Also, more customers and states are placing a value on greenhouse gas reductions,” noted Reed.
Today, fewer than two percent of U.S. transformers are made with amorphous steel cores, according to Metglas, and most grain-oriented electrical steel is imported from Asia. In addition to improving energy efficiency, a shift to using amorphous steel produced in the United States would help address concerns in the utility sector over transformer availability and long delivery times. There has been a severe shortage of transformers due to global supply chain disruptions, which were exacerbated by the pandemic.
Reed says higher efficiency standards would encourage greater U.S. production of amorphous steel to help offset geopolitical tensions and shipping delays. "Working to address near-term supply chain challenges and strengthen domestic manufacturing of key components in the electric grid” is cited by DOE as a key benefit of updated standards. Reed agrees: “If implemented as written, [the updated standards] will bring hundreds of steel manufacturing jobs back to the United States, promote local manufacturing, and expand local economies.”
Energy efficiency delivers multiple benefits: cost savings, lower greenhouse gas emissions, millions of jobs, and—in the case of the electric grid—less stress and strain on an energy system that the country depends on to be safe, reliable, and resilient. “I don’t see challenges,” explains Reed. “I see opportunities! Opportunities for Metglas to work with utilities, transformer manufacturers, and DOE. And to improve the U.S. electrical grid, reduce the delivery times that utilities are seeing for transformers, and bring high-paying jobs back to the United States.”
We'll deliver a dose of the latest in environmental policy and climate change solutions straight to your inbox every 2 weeks!
Sign up for our newsletter, Climate Change Solutions, here.
1020 19th Street, NW, Suite 400 Washington, DC 20036-6101
info@eesi.org Staff directory EIN: 52-1268030
EESI advances science-based solutions for climate change, energy, and environmental challenges in order to achieve our vision of a sustainable, resilient, and equitable world.

Large Power Transformers Copyright © Environmental and Energy Study Institute (EESI). Our work is licensed under a Creative Commons Attribution License. Privacy Policy