Alloy Enterprises raises $26M for aluminum fabrication at scale.
The Mitsubishi AZ600 melts welding wire with a laser beam to create high-quality 3D structures, producing high-speed, high-precision 3D printing (3DP) while reducing energy consumption and waste. Copper Wire Machine
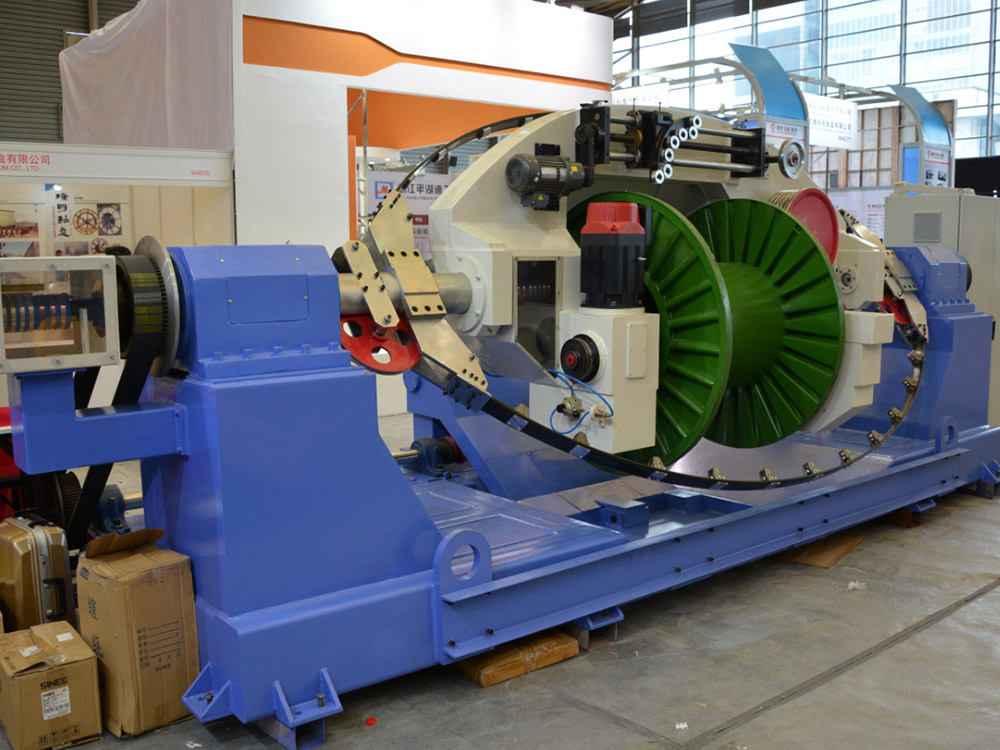
Applications include rapid prototyping, mold and die, one-offs, short runs, mass manufacturing, maintenance, repair, tooling, and more.
With the same proprietary wire-feeding technology used in Mitsubishi’s wire EDMs, a simple command on the machine’s CNC control feeds the exact amount of wire to the target location. Unlike other 3DPs, the wire is in the front of the machine so it’s easier to replace.
Wire-laser metal 3DP is a more efficient and versatile process than powder-based metal 3DP. It offers higher deposition rates, better surface finish, reduced porosity, better mechanical properties, and reduced powder waste.
Additionally, wire-laser metal 3DP is safer to operate because it doesn’t use potentially flammable and explosive powder. And, because wire-laser metal 3D printing is a closed system, the metal is contained within the printer, reducing the risk of operator exposure.
Alloy Enterprises, the world’s first Digital Aluminum Fab, announced the completion of a $26 million oversubscribed Series A round led by Piva Capital and joined by new investors Unless, Flybridge Capital, MassMutual Catalyst Fund, Robert Downey Jr.’s Footprint Coalition, and existing investors Congruent Ventures and Riot Ventures. The funding brings the total raised to $37 million.
Demand for aluminum has been escalating, driven by lightweighting for e-mobility across the transportation sector and the need for more sustainable materials. Aluminum is infinitely recyclable; it has twice the strength-to-weight ratio of steel and is an ideal material for lightweighting. Aluminum components will be part of the electrification journey of everything that moves.
However, the U.S. has lost a third of its foundries. Traditional manufacturing processes, such as casting, aren’t keeping pace with the speed of innovation.
Alloy Enterprises is filling the void with a fast, cost-effective manufacturing method that streamlines production of complex aluminum parts at scale in the U.S. The solution is a process specially designed for aluminum that doesn’t use aluminum powder. Using a combination of laser cutting and diffusion bonding, the team can produce production volumes through its machines cost-effectively while maintaining the advantages of 3DP, such as reducing lead times, iterating designs quickly, avoiding expensive tooling, and digitizing inventory.
Aluminum, especially alloys such as 6061, can be difficult and expensive to print using powder bed processes. The company developed its selective diffusion bonding process specifically for aluminum, for scale production. Its novel feedstock is already scaled and is produced in 10-ton runs. This summer, Alloy Enterprises will start delivering production volume parts. The company’s actively evaluating and qualifying new customer applications and has the capacity for volume production.
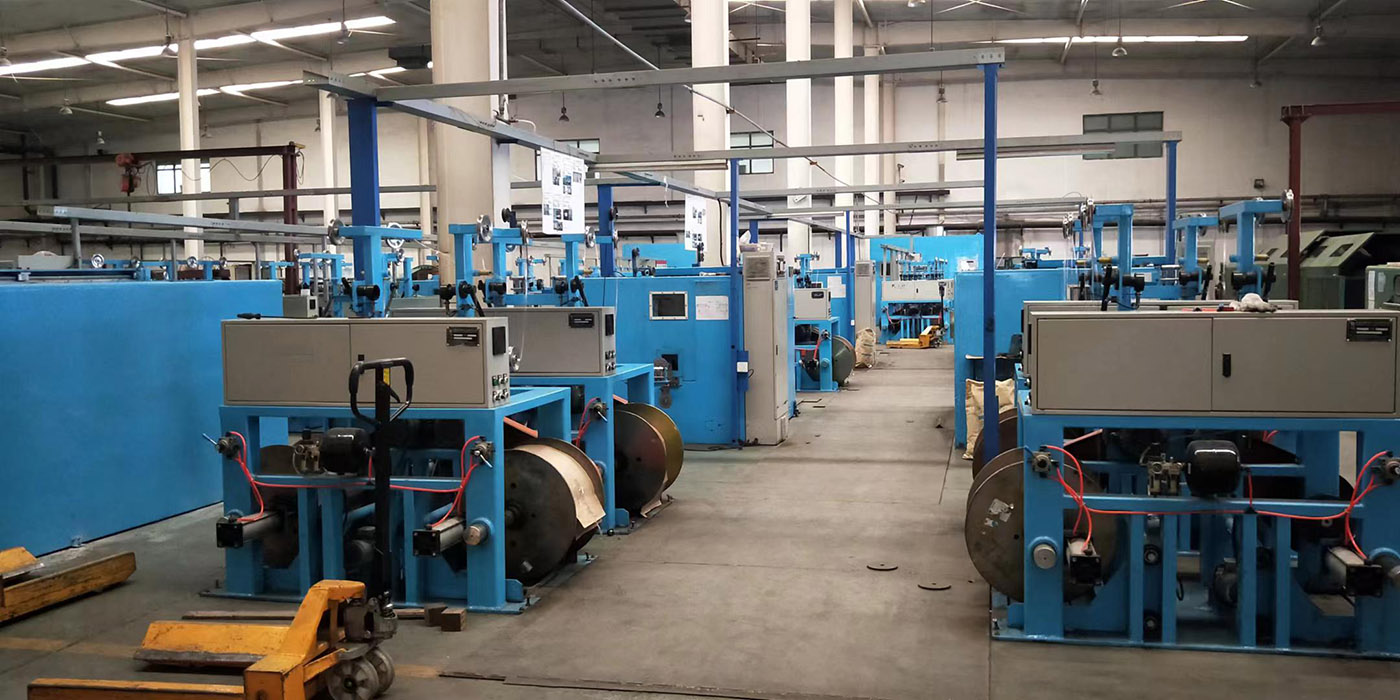
Cable Twisting Machine Check out more from this issue and find you next story to read.