This leveling machine with electromechanical gap control is used to destress and level these 1.57-in. (40-mm) parts.
Achieving flat and stress-free sheets or parts is essential in the metalworking industry for ensuring high-quality manufacturing. Water Proof Wire Connectors
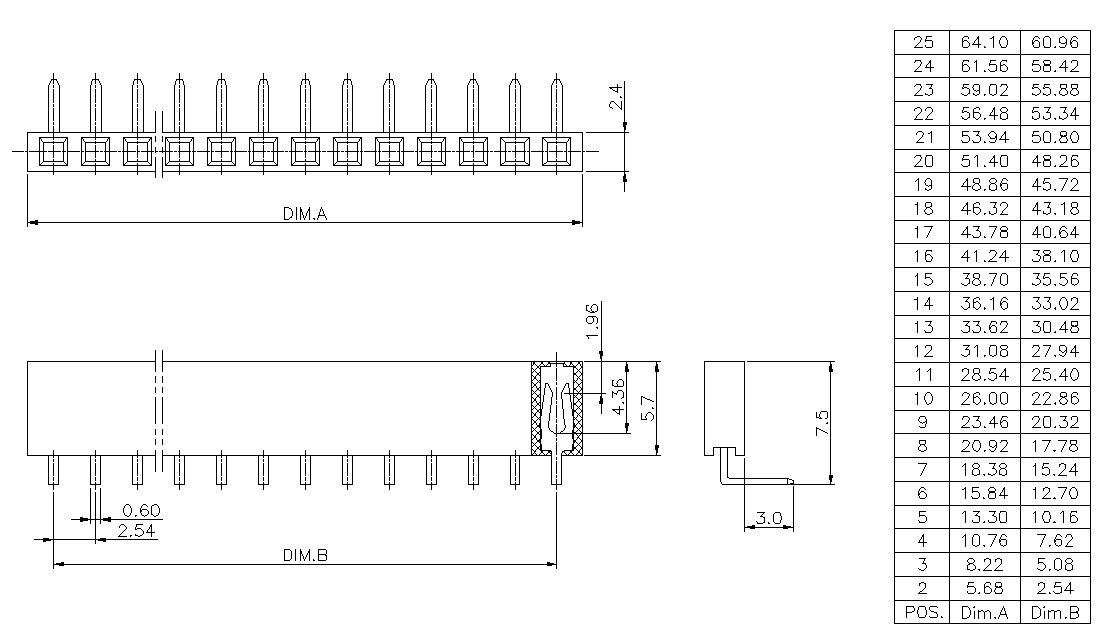
Roll leveling is a key process that eliminates flatness defects and internal stresses. Traditionally, hydraulic systems have been employed to control the leveling gap and counter the forces exerted during the leveling process. Today, leveling technology centered on electromechanical gap control is available and has the potential to minimize maintenance concerns and energy consumption.
Roll leveling is commonly used for both metal strips and flat metal parts, allowing for the removal of unevenness and tensions introduced during coil winding or previous treatments. Roll leveling machines employ upper and lower leveling rollers arranged in an offset configuration to guide the material through a serpentine-like line. This process involves initially bending the material beyond its yield strength, heavily plasticizing it and thereby eliminating undesired bends and tensions. Subsequently, as the material continues through the machine, it is bent a little less on each further leveling roller until the material is no longer plasticized by the time it reaches the last leveling roller, only deformed elastically. During this process, adjustable leveling gaps play a crucial role in accommodating variations in material thickness or bending moments, ensuring optimal leveling results.
As the material passes through the leveling gap, high counterforces arise within the machine. These forces tend to expand or open the leveling gap, necessitating robust design considerations for the rods and bolts that hold the machine frame in the desired position relative to one another. Previous approaches from manufacturers involved oversized components to withstand the forces, leading to increased weight and manufacturing costs.
Hydraulic systems have been conventionally used to compensate for the elongation of rods and maintain the leveling gap in part leveling machines. While hydraulic piston-cylinder units offer the required forces and response time, these systems can be considered complex and require regular maintenance. Some users also have concerns over their energy consumption.
To address the challenges associated with hydraulic adjustment devices in metal leveling, an electromechanical gap control system has been developed. This system replaces hydraulic components with electromechanically operated sliding wedges, providing advantages in machine structure, manufacturing costs, and maintenance requirements.
The electromechanical gap control system employs an electric motor, such as a three-phase servo drive, to drive the movement of the sliding wedge. Typically, this electric motor is coupled with a gear system, like a worm gear, which interfaces with a spindle responsible for displacing the sliding wedge. By using an electric servomotor, direct interaction with sensors or monitoring devices becomes possible. This enables real-time compensation of changes in the effective length of the rods. The adjustment mechanism simplifies control through conventional electrical systems, leveraging control electronics and sensor feedback for precise control over the amount of force applied, allowing for accurate and consistent leveling.
The electromechanical gap control system eliminates the need for hydraulic components, reducing energy consumption and maintenance costs. The sliding wedge design also generates high vertical forces with minimal horizontal forces, ensuring precise and efficient adjustment. Additionally, the system provides overload protection by limiting the compensation of rod elongation, safeguarding the leveling machine and its components, such as cardan shafts, from potential damage.
Electromechanical gap control provides a protective mechanism for the leveling machine when it is at risk of overstress or overload. Even in situations where the forces in the leveling gap reach potentially damaging levels, the electromechanical system can prevent material plasticization by partially reducing the compensation of rod elongation based on material-specific calculations. The independent movement of sliding wedges for each rod allows for this adjustment. While the leveling result for the current sheet or part might not be optimal, it is often still usable, effectively safeguarding the leveling machine against overload.
Although some believe that thin metals require a mechanical adjustment while thick metals necessitate hydraulic pressure, they are not correct. The choice between mechanical adjustment and hydraulic pressure is not solely dependent on the thickness of the metal being leveled.
Servomotor-driven sliding wedges are used to adjust the pressure applied to metal parts as they are processed through the leveling machine.
In the leveling process, the pressure requirements (tonnage) needed to destress and level material are influenced by various factors such as the material's properties, surface conditions, and the desired leveling outcome. While it is true that thin metals generally exert lower tonnage requirements compared to thicker metals, the choice between mechanical adjustment and hydraulic pressure should not be solely based on metal thickness.
Modern electromechanical gap control systems provide an effective and versatile solution for both thin and thick metals. Nonhydraulic machines are currently available that can handle metal thicknesses ranging from 0.024 in. (0.6 mm) to 2.6 in. (66 mm). These systems utilize servomotors and sliding wedges to precisely control the leveling gap, regardless of the material thickness. By monitoring the forces and adjusting the effective length of the rods, electromechanical systems can accommodate the specific requirements of the leveling process across a wide range of metal thicknesses.
Electromechanical systems can achieve high levels of power density and efficiency, providing fast response times and precise positioning capabilities.
Sales Manager, U.S. and Canada
See More by Dennis Ebner
Read more from this issue
Find The Fabricator on Facebook
Find The Fabricator on Twitter
The Fabricator is North America's leading magazine for the metal forming and fabricating industry. The magazine delivers the news, technical articles, and case histories that enable fabricators to do their jobs more efficiently. The Fabricator has served the industry since 1970.
Easily access valuable industry resources now with full access to the digital edition of The Fabricator.
Easily access valuable industry resources now with full access to the digital edition of The Welder.
Easily access valuable industry resources now with full access to the digital edition of The Tube and Pipe Journal.
Easily access valuable industry resources now with full access to the digital edition of The Fabricator en Español.
On this episode of The Fabricator Podcast, Philadelphia-based welder and trades advocate Pa'Trice Frazier joins host Dan Davis...
© 2024 FMA Communications, Inc. All rights reserved.

Moto Connector Not yet registered? Sign up